Aerospace Application
In aerospace engineering and related fields safety-critical
systems are developed. Simulations in every stage of the product
development cycle are becoming more and more complex. For example,
multidisciplinary coupled simulations or optimizations are being
conducted in distributed computing environments. In order to get
some level of confidence in the quality of the simulation results,
it is important to record the complete history of the computation.
Computer based simulation is used extensively in many
scientific and technical applications, for instance in the
development and design of aircrafts and motor vehicles, or in
forecasting the weather. In recent years, parallel computing has
been very successful in reducing the computing time required for
such modeling to acceptable levels. Nevertheless, the lack of
interoperability and transparency of the tools used in parallel
and distributed simulation systems still causes problems. With
more complex and multi-disciplinary problems, users tend to spend
much of their time configuring and connecting the tools needed for
one particular simulation than running the simulation itself. The
fields of development are diverging between the "traditional" HPC
programming paradigm (using Message Passing) and the success and
effort made with distributed object computing. In addition to the
focus on pure parallel performance of a simulation, an environment
for the process to run in is needed. TENT is an environment to
overcome these problems and close the gap.
The Simulation Integration Environment TENT
TENT
is a software integration and workflow management system that
simplifies work by means of simulation process chains in
distributed environments. In TENT all tools of a simulation can be
integrated and centrally started and controlled from a user's
desktop via a graphical user interface (GUI).
The major characteristics of TENT are:
Use of distributed computing resources (PCs, workstations,
clusters or supercomputers with scheduling systems, and
Computational Grids)
Visual presentation of workflows in a graphical user
interface (GUI) available on all systems
Flexibility in setup, configuration, online control and
online visualization of simulations
Integration of project-based data management including the
option of collaborative work
Monitoring and control of an ongoing simulation from any
computer
Simple integration of existing applications
Automatic, high-performance data exchange between all the
steps of a distributed simulation workflow
The TENT system is a component-based development using modern
software technologies and programming languages (Java, CORBA, XML, Python, WebDAV).
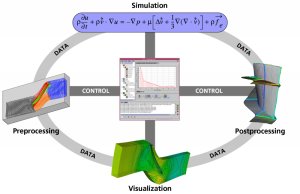
The SikMa Project
The DLR project SikMa
(Simulation of Complex Manoeuvres) is under the direction of the
DLR institute of Aerodynamics and Flow Technology (AS). The
objective is to develop an interactive simulation environment for
the simulation of a freely flying, fully configured, elastic
warplane. To implement the simulation, the aerodynamic, flight
mechanical and aeroelastic equation systems will be calculated for
every step, in a time-accurate coupling of aerodynamics, flight
mechanics and aeroelasticity.
In addition, the results from the SikMa project will drive the
idea of TENT, a uniform simulation environment for DLR, and
make a substantial contribution to the DLR core area of the
virtual aircraft. Along with the development of the interactive
integration environment, and the computing processes and coupling
algorithms, the SikMa project will conduct wind tunnel tests. The
tests include different models in various manoeuvre scenarios, to
obtain a comprehensive data set for the verification and
validation of the overall simulation environment.
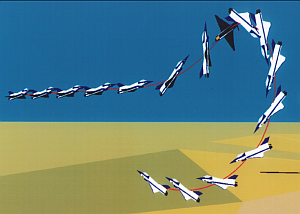
Provenance and TENT
The following gives an overview of how the Provenance Architecture is used to record information within the workflows of the simulation integration
environment TENT. The architecture records three kinds of information:
Interaction P-Assertions
Interactions between system components are
recorded as interaction p-assertions. They are used for the ability to restart processes,
track user access to data and control user access. In case of a
computational job being rejected (by a utilized batch system or
Grid) the system has to recognize and record this to the
provenance store, and notify TENT for re-submission of the
job. Workflow control information and data interchange between
system components as well as input files for both - CFD and
aero-elastic codes - need to be identified and recorded.
Relationship P-Assertions
Interaction p-assertions between participating components and actors of a
process are vital for the documentation of process. But
additional information is needed to connect these interactions
through causality or other relationships to yield a continuous
chain of pieces of information to fully describe the processe's
and data provenance.
Relationship p-assertions achive this by recording the relationships between a component's inputs and outputs.
Actor State P-Assertions
For reasons of reproducibility, version information about the
algorithms used and computational codes must be tracked along
with the data itself. This form of information is recorded in actor-state p-assertions.
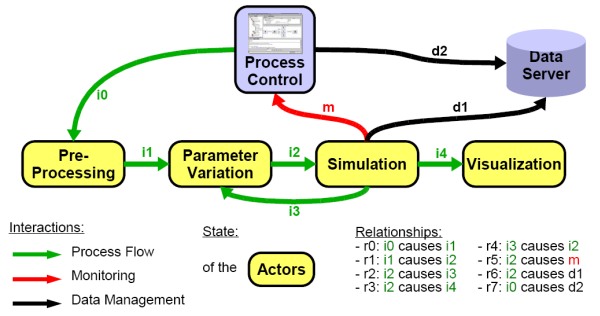
Provenance Queries
The process documentation recorded precisely documents processes. This leads to the possibility to ask questions about the
provenance of a processes recorded for analysis purposes. In the
following a set of potentially useful provenance queries are presented that makes use of the
previosuly recorded process documentation.
For a better understanding, disambiguities on the terminology
must be clarified. Previously only the synonym
"simulation" has been used. As a simulation may be
run using varying parameters and configurations, to distinguish
between simualtions, the term "case" is be used to identify a particular
configuration of an aerodynamic simulation. This
includes the configuration of relevant aerodynamic parts in a
certain physical arrangement, and prescribed by specific physical
boundary conditions. Every case may be simulated multiple times
with changing boundary conditions and possibly changing geometries
(e. g. flap settings).
-
Given a certain item of result data, from which case
has it been obtained?
-
What is the history of a given data item?
Given a certain configuration, how often has it been
simulated?
-
How many/what data items have been obtained as the result of
a configuration?
-
Given a certain aerodynamic part, from which cases has
this part been simulated?
Given certain boundary conditions, in which cases have they
been applied?
Benefits
For the aerospace application, the integration of the Provenance Architecture has the following benefits:
-
A clean documentation of simulation workflows that are
distributed in multiple/separated network domains and of
properties of used resources.
-
The ability to analyze and reason over all conducted
computations. This includes the ability to compare computations
(e. g., for extraction of similarities or differences), the
ability to easily retrace and understand computations and their
results, and the possibilty to support the analyses using
tools.
-
It allows checking for requirements. For example, it allows
checking for compliance to legal and business regulations, or
conformance to internal research standards ("Best
Practices").