Automotive engineering application
Water radiators, oil coolers, intercoolers, oil-water heat exchangers,
diesel oil coolers and gearbox oil coolers are a few examples among the variety
of heat exchanger applications in automotive engineering.
The numerical simulation of such devices demands for the combined
calculation of fluid flow and solid body heat conduction. The integration of
such simulation into the virtual design process of engines requires fast
numerical methods, based on a parameterised CAD representation and
semi-automatic mesh generation.
 |
Fig. 1: Oil-water heat exchanger
|
 |
Fig. 2: Components of the heat exchanger
|
Figure 1 shows the configuration of a typical oil-water heat exchanger. The
device is built in several layers, every second supplied with water and oil
respectively. The CAD representation of the individual components is
represented in figure 2. To increase the rate of heat transfer, turbulence
generators are placed in the flow path, which results in a complicated flow
geometry.
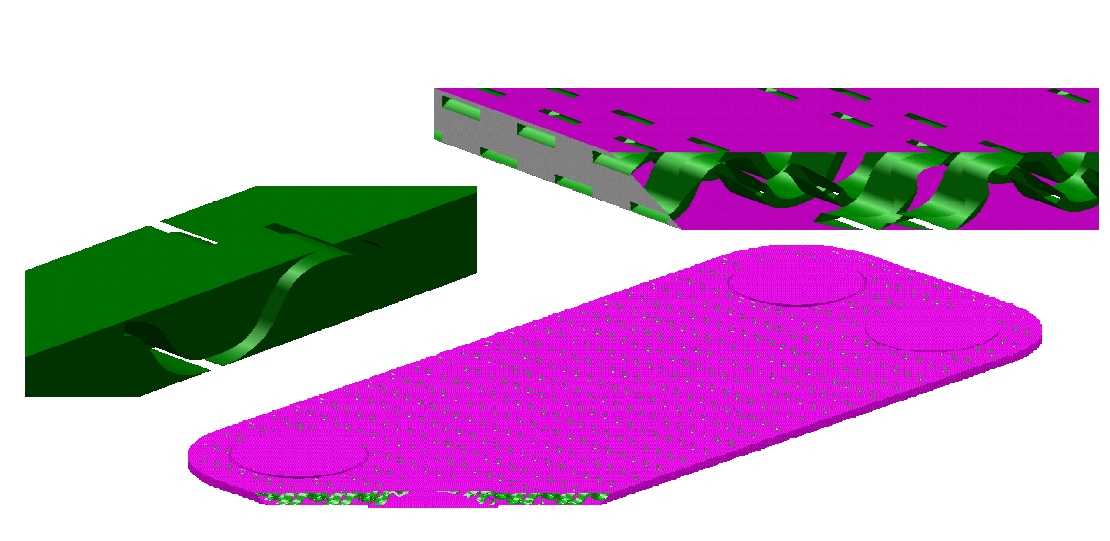 |
Fig. 3: Fluid domain
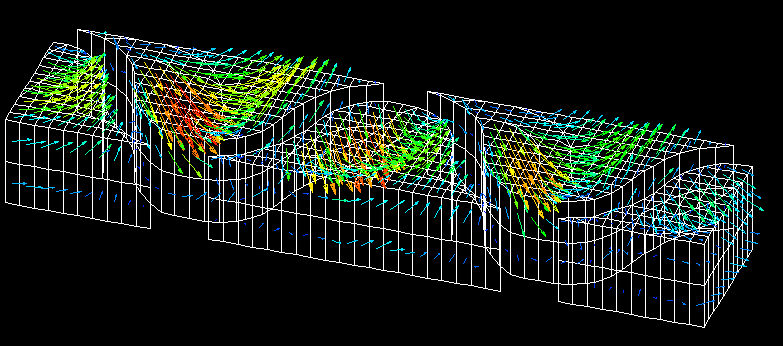 |
Fig. 4: Details of the fluid velocity vectors
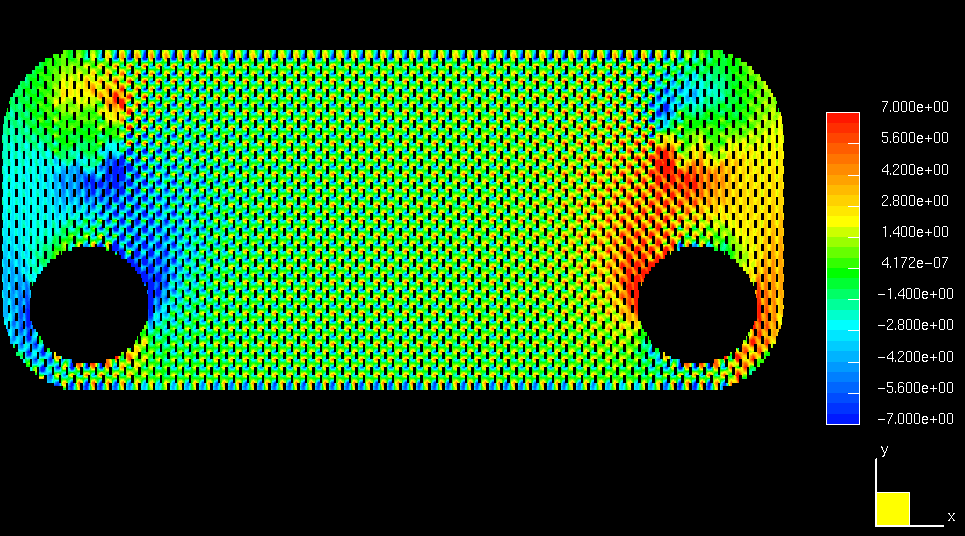 |
Fig. 5: Distribution (velocity component perpendicular to the main flow
direction
Figure 4 displays details of the fluid velocity vectors. Figure 5 gives an
impression of the fluid velocity distribution (velocity component perpendicular
to the main flow direction).